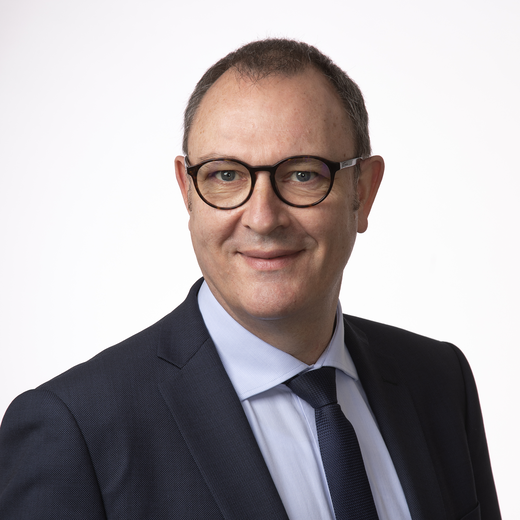
Frédéric Loiseau
Head of Sales
+33 2 28 21 08-28
Manutention de produits en vrac dans le process de compoundage